產品詳情
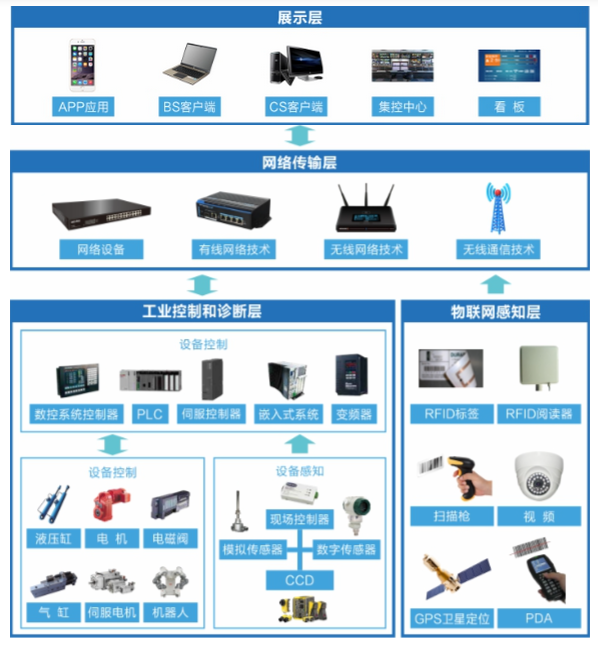
第一步:工廠現場調研
車間布局、工藝流程、生產設備現狀、設備維護保養(yǎng)計劃與維保記錄、設備巡點檢操作規(guī)范、設備開停運行情況、設備故障處理過程、生產操作、設備需求(自動化設備等)、設備接口與協(xié)議、設備相關的關鍵數據采集、優(yōu)化潛在工位的操作人員訪談、自動化改造部門的歷史項目、在建項目、規(guī)劃項目、自動化改造部門產品穩(wěn)定性及自控水平……
1.現場網絡傳輸搭建

通過對人機交互終端搭建可以將生產計劃指令、設備日常維護指令直接下達到設備上,并且對于設備的實時運行情況、單臺設備的OEE做圖像化展示,還可實現加工產品與設備的信息共享。設備終端還將包括:調用SOP作業(yè)指導書、調用工藝圖紙、人員上崗驗證、人員考勤、安燈預警操作等相關功能,提供了生產線設備端的交互入口,讓人、機、料互相交互成為可能,操作人員按相關指令進行作業(yè)任務,進而減少溝通成本、保障按計劃有序開展工作;集成了崗位驗證、考勤功能,簡化了人員管理的運營成本。

4.標簽的使用
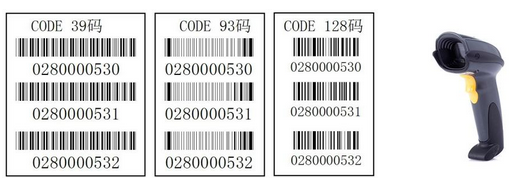
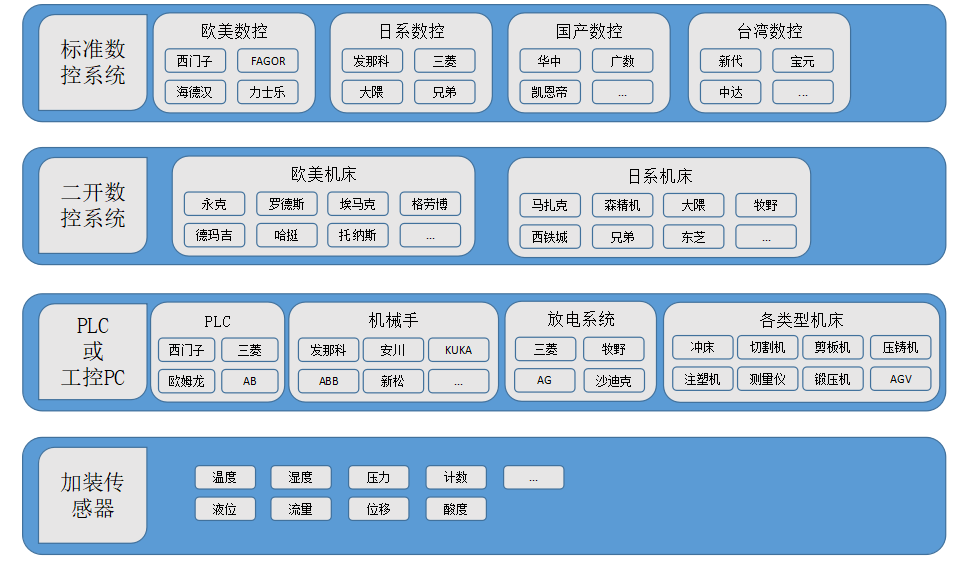
原則上應在每個CNC數據機床工位加裝視覺圖像識別系統(tǒng),在吊鉤上取得在制品放到工位上時進行視覺圖像自動識別,系統(tǒng)識別后自動調用相關的加工程序到對應加工設備,如果考慮每臺加工設備都加裝視覺圖像識別系統(tǒng)成本問題,可以考慮規(guī)劃生產流水線。僅在每流水線的特定位置加裝一套識別系統(tǒng),系統(tǒng)識別在制品后,能夠通過流水線把相應在制品指定分配到對應的加工設備上,這樣亦可進行自動裝載程序,并且可以做到按CNC工位的繁忙情況智能均衡安排加工設備的生產任務,避免加工不同型號產品時刀具的反復切換帶來的時間成本。
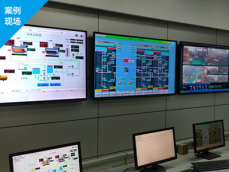
2.對生產線的每臺生產設備(包括PLC,CNC數控機床等)部署設備終端,再通過企業(yè)已存在的網絡將數據進行統(tǒng)一聯網,從而形成對設備的實時監(jiān)控,采集計算設備實際執(zhí)行OEE的相關數據,從而為每臺設備制定 OEE計劃標準,將標準集成到系統(tǒng)中
3.通過構建設備基礎資料,設備運行監(jiān)控,設備運行保養(yǎng),設備備件管理體系,有效保障設備相關的所有管理需要
4.可視化車間看板,異構件備料看板、物流(裝車)計劃看板、生產指令看板、快速返修看板、在制品流量監(jiān)控看板、異常看板、庫位目視化看板、差異看板、消滅看板等的運用
5.安燈系統(tǒng)異常管理。通過操作輔助設備主動匯報異常(例如PDA進行異常匯報),自動發(fā)送郵件,短信,看板等方式展現給相關負責人員
6.多維度的KPI考核數據客觀反饋設備以及相關管理人員的績效;
7.生產運營集控中心的建立。在企業(yè)內部構建生產運營集控中心。將差異化看板系統(tǒng)、設備聯網監(jiān)控系統(tǒng)、安防監(jiān)控系統(tǒng)、異常預警系統(tǒng)統(tǒng)一集成部署到運營集控中心,使管理者在一個地方實時匯總現場數據,作出管理決策。

分布式數據架構、滿足集團需求
實時訪問全廠生產數據
高效的數據壓縮算法
長期保存歷史數據
支持在線計算和統(tǒng)計
支持遠程范圍、多種數據接口
個性化定制服務、靈活滿足用戶需求
不間斷穩(wěn)定運行
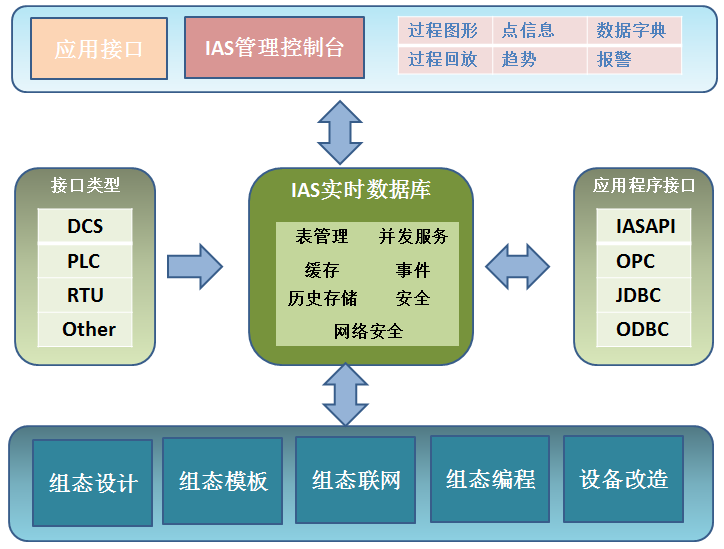
專業(yè)的圖形仿真技術
監(jiān)控畫面與實際生產活動保持一致
豐富的設計工具
工程組態(tài)模板(采集模板、畫面模板、腳本模板、圖形模板)
組態(tài)工程開發(fā)XML
多語言操作系統(tǒng)兼容
支持完整的PLC協(xié)議
具備定制化組態(tài)能力
可進行設備改造、信號轉接
2.將每臺設備的指令直接下達到具體設備,操作人員按相關指令進行作業(yè)任務,減少溝通成本、保障按計劃有序開展。
3.集成監(jiān)控檢測加工設備關鍵指標,避免質量異常發(fā)生,節(jié)省了返工成本
3.集成了安燈系統(tǒng),支持在安全、人員、質量、響應和成本方面的不斷改進,減少浪費
5.與CNC工位相互結合,提升了生產數據交互的穩(wěn)定性,避免異常的發(fā)生。
6.設備日常維護作業(yè)計劃由系統(tǒng)自動產生,防止遺漏延期,確保計劃正確執(zhí)行,減輕維修部門主管工作,提高了人員的工作效率;
7.設備日常維護作業(yè)有序進行,保障了設備的穩(wěn)定性,降低了生產風險、降低了設備維修成本。
8. 設備管理系統(tǒng) OEE的最大優(yōu)化。時間稼動率(可用率),性能稼動率(表現指數),良品率(質量指數)
9.可視化車間看板。通過多維度的統(tǒng)計、分析、計算為管理者提供企業(yè)數據的可視化展示,實現目視化管理,從而降低企業(yè)運營成本,提升各個業(yè)務部門協(xié)同效率。
五、MDC數據采集系統(tǒng)的應用場景
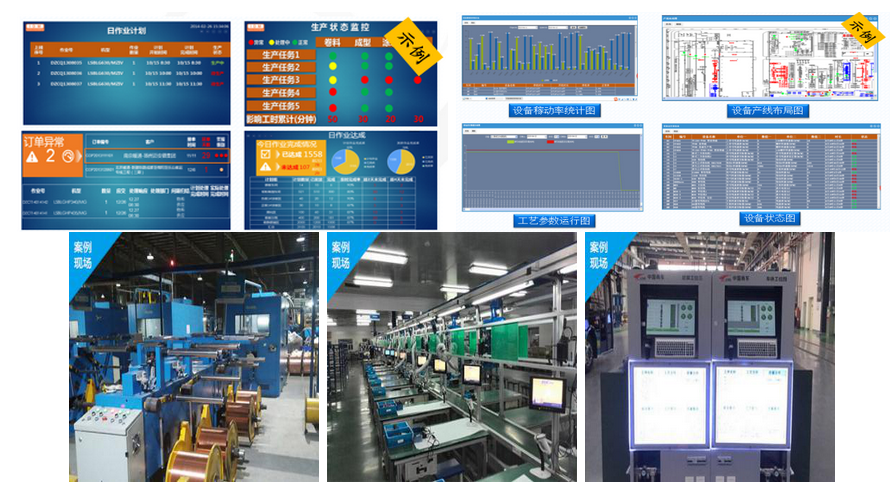
六、應用的案例
1.浙X催化劑工廠生產數據采集系統(tǒng)

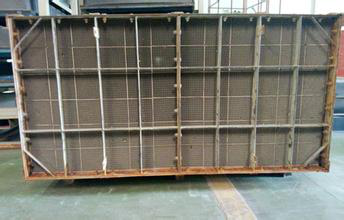
本項目主要實現的功能包括:生產計劃排程、生產信息管理、數據采集、設備管理、差異預警管理、看板管理、物資管理、項目信息管理、集控中心、實時數據庫子系統(tǒng)、二次安全防護子系統(tǒng)、ABB機器人通訊、視覺識別子系統(tǒng)、組裝模塊掃碼子系統(tǒng)
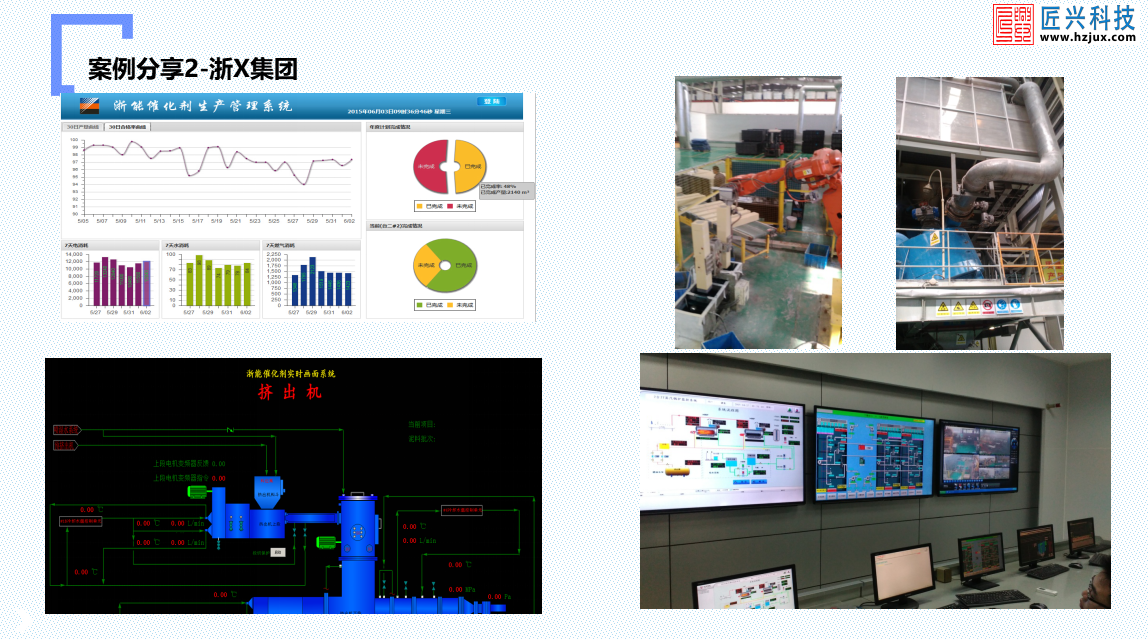
1、實現通過二維碼生產業(yè)務和質量的全過程追溯,生產效率提升17%,品質問題降低38%
2、實現所有客戶可以隨時通過系統(tǒng)了解訂單生產進度狀況,客戶滿意度增加75%
3、實現所有設備運行狀況實時采集,實時展示,實時監(jiān)控,實時預警,設備效率增加31%
4、實現安全庫存即時預警,物料及時率提供42%
5、實時管控物料配送到貨狀況,物料供貨準時提供67%
6、實現和機器人的實時通訊,識別率提高到99.87%
2.中國X車工廠生產數據采集系統(tǒng)
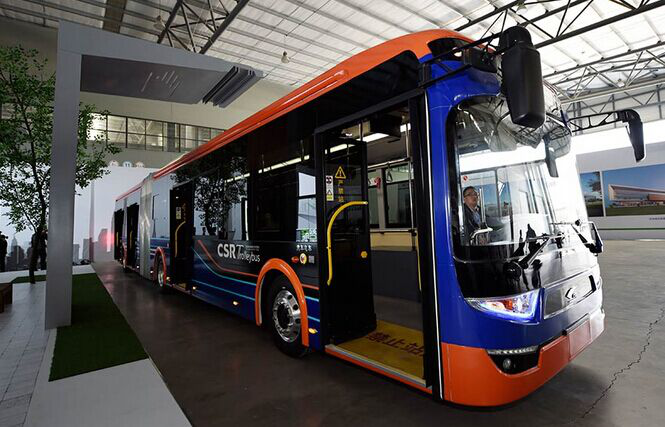
本項目主要實現的功能包括:計劃排程、生產管控、供應鏈管控、數據采集、異常管理、質量溯源、可視化等
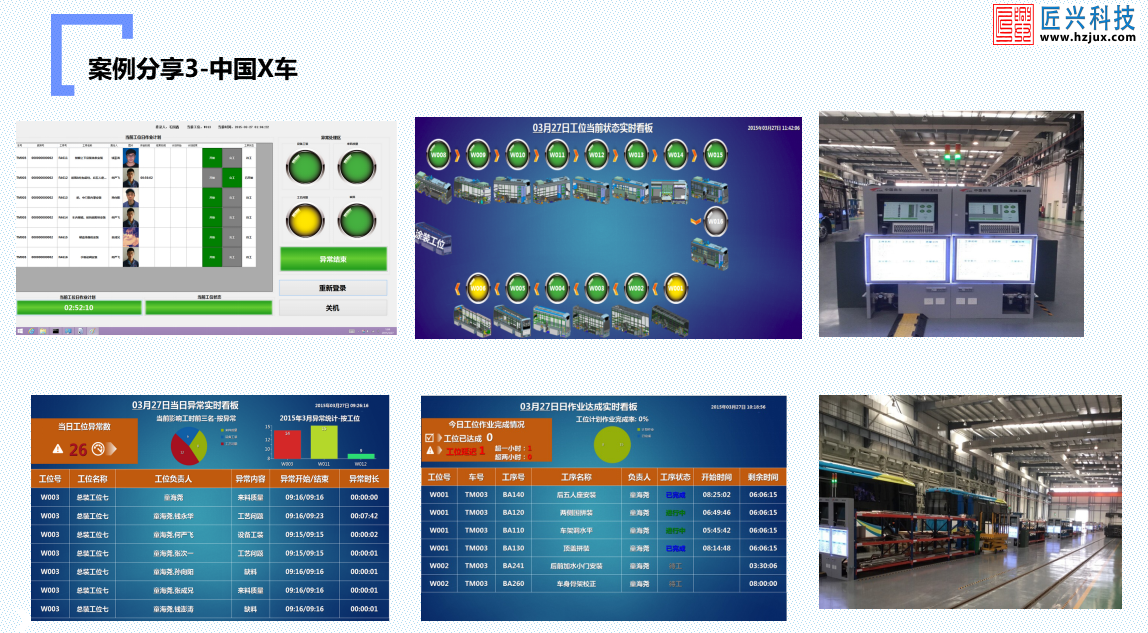
制造過程數字化與透明化,對決策的準確制定提供了很大支持,保障持續(xù)的盈利能力;
智能化的管理技術,改善原有傳統(tǒng)模式對人員經驗與素養(yǎng)的依賴,快速帶動管理升級;
任務發(fā)布與接收更加及時透明,確保員工準確及時按指令執(zhí)行,同時對執(zhí)行結果做有效監(jiān)控跟蹤;
目標與實際狀況之間的差異,層級化的異常處理方案,確保PDCA的循環(huán)改善
降低或消除數據統(tǒng)計時間36%;
縮短生產提前期8%;
提高產品合格率5%;
提高產線交接班效率67%;
生產效益提升10%;
3.圣XX床上用品集團工廠生產數據采集系統(tǒng)

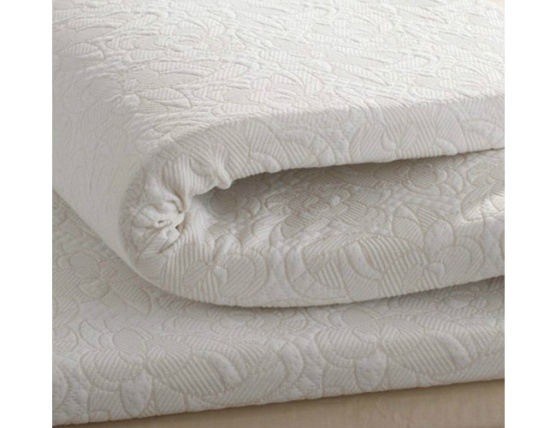
本項目主要實現的功能包括:計劃排程、生產管控、 RFID實時供應鏈系統(tǒng)、數據采集、設備管理、異常監(jiān)控系統(tǒng)、質量溯源、可視化等。

1 、異常實時發(fā)布,機修維護受到監(jiān)控,減少異常發(fā)生的浪費時間10%
2 、設備保養(yǎng)執(zhí)行過程由系統(tǒng)監(jiān)控,延長設備的使用壽命,節(jié)省設備費用20%
3 、實時監(jiān)控產線執(zhí)行計劃,縮短生產節(jié)拍。
4、 物流運作智能執(zhí)行,減少物流流轉的浪費時間5%
5 、RFID產品全過程追溯,提高客戶對產品的滿意度,銷售效益提高0.3%
6、周計劃到日計劃 細化的完善,計劃實現實時下達到各工位,并反饋實時數據到計劃人員,減少跟單員的人數4名
4.超X電池集團公司工廠生產數據采集系統(tǒng)
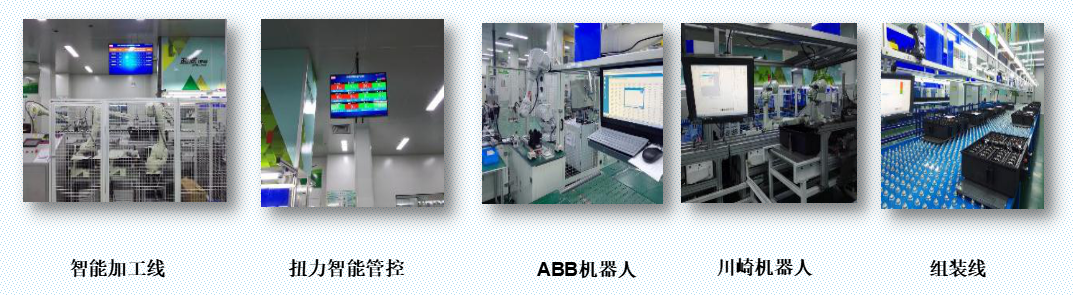
實時模塊:流水線數據采集、條碼管理、生產管理、質量管理、包裝管理、溯源管理、預警管理、可視化管理等
1、實時反應生產流程過程中的問題,及時反饋并由操作人員進 行及時處理解決,整個產線對異常的處理和響應速度提高了72%
2、具備了整體協(xié)同能力,提高預測、計劃和生產調度方面的科 學性、準確性和及時性,車間在制品降低了9.6%,生產成本降 低4.2%
3、為現場操作人員與上級管理人員提供即時信息反饋,確保更 快、更好的完成生產任務,生產效率提高8.3%
4、能監(jiān)控在制品在任意時刻的位置和狀態(tài),實時收集相關數據從而對每個產品形成可追溯性記錄,在出問題時可以快速查找問題所在
5.某大型家電企業(yè)(重慶)-家電行業(yè)工廠生產數據采集系統(tǒng)

主要實現的功能包括:生產計劃管理、供應商協(xié)同平臺、采購管控、智能倉儲、智能物流、智能生產、條碼識別管理、追溯管理、異常預警管理、報表管理、數據采集、看板管理、車間物料識別子系統(tǒng)、KPI體系。
1 、從訂單、生產、供應鏈整體協(xié)同度提升60%
2、訂單交期延誤率從35%下降至12%
3、人員執(zhí)行力提升70%
4、設備利用率提升22%
5、客戶滿意度提高30%
原文網址:http://www.hzjux.com/shengchanshujucaiji/